Sign in to follow this
Followers
0
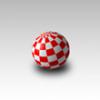
Окраска автомобилей в древности
By
Zak, in Статьи для наполнения сайта
-
Recently Browsing 0 members
No registered users viewing this page.
By
Zak, in Статьи для наполнения сайта
No registered users viewing this page.
Используя этот сайт, вы соглашаетесь с нашими Terms of Use.